Zakovica
Zakovica ili zakivak je mašinski element namijenjen za stvaranje nerazdvojivih spojeva. Na jednom kraju zakovice nalazi se glava (industrijska glava zakovice), a drugi kraj je klin cilindričnog oblika. Koriste se tako da se stave u rupu koja je već izbušena u materijalima koji treba da se spoje, a zatim se deo zakovice koji je prošao kroz rupu deformiše delovanjem sile, tako da se zakovica više ne može izvući. Zakovani spojevi su nekada bili osnovni vid spajanja metalnih delova. Danas su ostali osnovni vid čvrstog spajanja nekih lakih legura (duraluminijum), i posebno u avionskoj idustriji.[1] Spoj zakovicama dobro podnosi naprezanja po osi normalnoj na osu zakovice (smično naprezanje), dok su za naprezanja u smeru ose tela zakovice bolja rešenja vijci i matice.[2] Materijali za izradu zakovica su čelik, aluminijum, njihove legure a ponekad i drugi laki metali. Pre izvođenja spoja, sastoje se od tela zakovice (stablo) i nasadne (gotove, završene) glave. Posle deformacije u spoju uz ova dva dela postoji i završna glava koja drži spoj i zakovicu da ne ispadne iz rupe.



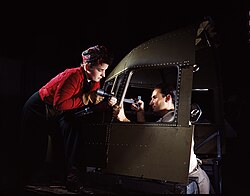


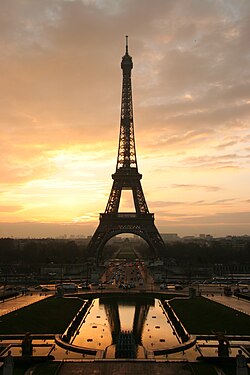


Zakovične spojeve su istisnuli vijčani spojevi. Bušenje rupa i zakivanje iziskuje generalno veći utrošak rada. Zavareni delovi su jednostavnijeg oblika, laganiji su i nisu oslabljeni rupama. Samo se još ponekad uzima zakovični spoj, koji inače vredi kao bezuslovno siguran spoj, naročito u gradnji s lakim metalima.[3]
Zakovice su mašinski delovi koji se sastoje od svornjaka (tela) i glave, takozvane gotove ili temeljne glave. Druga glava, nazvana završna glava, oblikuje se tokom operacije zakivanja. Izrada provrta na delovima koji se spajaju izvodi se probijanjem ili bušenjem. Prvi je brži i isplatljiviji (ekonomičniji), ali postoji opasnost od pojave pukotina na rubovima provrta. Bolje je naknadnim bušenjem ili razvrtanjem proširiti manji provrt na konačnu meru. U kvalitetnim konstrukcijama (čelične konstrukcije, kotlovi ili generatori pare) primenjuje se isključivo bušenje. Rubovi provrta na spoljašnjoj strani spoja moraju kod većeg prečnika zakovica biti skošeni. Za postizanje ispravnog zakovičnog spoja, provrti na delovima koji se međusobno spajaju izvode se tako da se ti delovi nalaze u privremenom montažnom spoju ostvarenom s pomoću vijaka, zatega i slično.
Zakivanje može biti hladno kod upotrebe mesinga, bakra ili lakih legura kao i čeličnih do prečnika manjeg od 10 mm. Toplo zakivanje izvodi se čeličnim zakovicama zagrijanim do svetlocrvenog žara (oko 1 000 °C). Za zagrejavanje zakovica služe peći ložene drvenim ugljenom ili koksom. Najprikladnije je električno ili plinsko zagrejavanje zakovica.[4]
Zakivanje
urediZakivanje je nerastavljivo spajanje limova i drugih tankostrukih konstruktivnih delova. Najčešće se koristi u lakogradnji (vazduhoplovne i slične konstrukcije) s materijalima kojima bi se zavarivanjem bitno smanjila čvrstoća (na primer aluminijumske i titanijumske legure), a katkada i u čeličnim konstrukcijama (visokogradnja, dizalice, mostovi) pri posebnim uslovima ugradnje (montaže). Izvodi se zakovicama, to jest metalnim trnovima s osnovnom glavom izvedenom na jednoj strani. Zakovice se umeću u bušene ili probijane otvore delova koji se spajaju, pa se na slobodnoj strani plastično oblikuju (zakivaju) u takozvanu završnu glavu, čime se postiže čvrsta veza spoja. Sve se zakovice zakivaju u hladnom stanju, osim čeličnih debljih od 10 mm, koje se prethodno greju približno na 1 000 ℃. Glava zakovice može biti poluokrugla, lećasta, upuštena ili plosnata, a struk pun ili šupalj. Završna se glava oblikuje posebnim alatima, ručno, hidraulički ili pneumatski.[5]
Kada je kraj trna koji se zakiva nedostupan (spajanje delova s polušupljim ili šupljim profilom), primenjuju se takozvane slepe zakovice,[6]koji oblikuju završnu glavu povlačenjem umetnutog trna u šuplji struk (povlačenjem zakovica), ili povlačenjem i sečenjem trna (tzv. POP-zakovice, nazvane po zaštitnom znaku američke kompanije „Emhart“, koja je prva započela proizvodnju njih). Nepristupačni kraj struka takođe je zakivan eksplozivno (eksplozivne ili termičke zakovice), pri čemu dodirivanje glave zakovice posebnim alatom izaziva paljenje eksploziva umetnutog na kraj struka. Zakovice su u zglobu opterećene rezom (smicanje]), a prema broju poprečnih preseka u kojima se javljaju smičuća naprezanja, spoj je jednorezan (kada su dva dela spojena) ili višeseci.[7]
Zakivati se može ručno (uz upotrebu ručnog alata, odnosno pneumatskog ili električnog čekića) ili mašinski. Ručno zakivanje ograničeno je na slučajeve kad je obim posla mali i kad je prečnik zakovica manji od 26 mm, jer iznad toga, naročito kad su svornjaci zakovica dugi, snaga čoveka nije dovoljna za postizanje prikladne deformacije čitavog tela zakovice. Postupak pri ručnom zakivanju vrlo je jednostavan. Ugrejana zakovica se brzo uvuče u provrt, pa se na osnovnu glavu pritisne kalup podmetač (pridržač). Brzim udarcima čekićem najpre se zadeblja nasuprotni kraj svornjaka, pa se namesti kalup glavičar (oblikač), preko kojega se zatim nastavi udarati čekićem do konačnog oblikovanja završne glave. Mašinsko zakivanje se izvodi posebnim mašinama za zakivanje. Tim se načinom postiže veći i jednoličniji pritisak na svornjak zakovice, te se zakovica sabija po celoj dužini i bolje popunjava provrt. Brzina rada je mnogo veća, a posebni uređaj osigurava bolje priljubljivanje delova koji se spajaju. Glavni nedostatak je u tome što se često ne može primeniti na mestu montaže konstrukcije.
Osim dobrog ispunjavanja rupe u ispravnom zakovičnom spoju, završne glave zakovica moraju biti potpuno oblikovane, moraju dobro nalegati na površine delova u spoju i ne smeju imati napukline.
U slučajevima kad zakovičasti spojevi ne smiju da dozvole prolaz fluida (na primer zidovi spremnika ili rezervoara, limovi parnih kotlova, oplate brodova i slično), nepropusnost je bezuslovan zahtev koji se na njih postavlja. Da bi se nepropusnost zakovičnih spojeva u takvim slučajevima još više osigurala, njihova izrada uključuje još i takozvano podbijanje (zaklepanje) kao završnu operaciju. Ta operacija sastoji se u priljubljivanju krajeva limova i glava zakovica posebnim alatom, takozvanim podbijačima čiji završetak mora biti malo zaobljen. Radi toga rubovi delova koji se spajaju moraju biti zakošeni pod uglom od 15 do 20°. Pri tome ne sme doći do oštećenja limova alatom, jer to može izazvati njihovo nedopušteno slabljenje. Podbijanje je izvedivo samo kad je debljina limova veća od 5 mm. Osim tih glavnih postupaka zakivanja u praksi, postoje i neki posebni pri kojima se obično upotrebljavaju posebne (specijalne) vrste zakovica.
Zakovične spojeve istiskuju sve više zavareni spojevi. Bušenje rupa i zakivanje iziskuje, generalno uzevši, veći utrošak rada. Zavareni delovi jednostavnijeg su oblika, laganiji su i nisu oslabljeni rupama. Samo se još ponekad uzima zakovični spoj, koji inače vredi kao bezuslovno siguran naročito u gradnji s lakim metalima (posebno s aluminijskim legurama).
Prednosti i nedostaci zakovičnih spojeva
urediPrednosti zakovičnih spojeva:[8]
- materijal se ne oslabljuje toplotnim uticajima, a nema niti opasnosti od puzanja;
- mogu se spajati različite debljine materijala, te materijali s presvlakama, kao i različiti materijali;
- kontrola kvaliteta je jednostavna;
- trenje u spoju dovodi do prigušenja vibracija i buke;
- velika brzina izvodenja za neke vrste zakovica, pa kod ugradnje zamjenjuje vijke;
- spoj se ponekad može i rastaviti.
Nedostaci:
- rupe oslabljuju konstrukciju;
- neravnomerna raspodela naprezanja;
- potrebno preklapanje delova spoja;
- kod različitih materijala može se javiti kontaktna korozija.
Podela
urediZakovice dijelimo na sitne (sa prečnikom do 10 mm) i krupne (sa prečnikom od 10 do 37 mm). Prema obliku glave, sitne zakovice mogu biti sa: poluokruglom glavom, upuštenom glavom, pljosnatom glavom, trapeznom glavom i sočivastom glavom. Po načinu postavljanja mogu biti obične, gdje je pristup omogućen i sa druge strane spoja prilikom postavljanja, i slijepe (slepe) kod kojih nema pristupa drugoj strani spoja pri postavljanju.
Prema položaju limova mogu biti sučeoni (imaju podmetače) i preklopni. Prema broju redova zakovica mogu biti jednoredni i višeredni. Prema rasporedu zakovica mogu biti sa paralelnim i cik-cak rasporedom. Prema broju ravnina smicanja zakovica mogu biti jednosječni i višesječni spojevi.
Postavljanje
urediU najvećem broju slučajeva koriste se posebni hidraulički ili pneumatički čekići za zakivanje. Ručni alat za zakivanje slijepih zakovica je u vidu alata sličnog kliještima. Mekane zakovice se mogu postaviti i čekićem, kojim se udara po stablu van rupe sve dok zakovica nije čvrsto postavljena i stvori se završna glava.
Ilustracije
uredi-
Tipična konstrukcija zakovicama.
-
Zakovični spojevi na željezničkom mostu.
-
Dvorezni i višerezni zakovični spojevi.
-
Slijepe (slepe) zakovice, koje se zakivaju s jedne strane spoja.
-
Alatka za zakovice.
-
Zakivanje običnih zakovica sa jedne strane spoja.
Vidi još
urediReference
uredi- ^ Heintz, Chris (2010). Flying On Your Own Wings. ISBN 978-1425188283. Arhivirano iz originala 2017-07-10. g.
- ^ "Elementi strojeva", Karl-Heinz Decker, Tehnička knjiga Zagreb, 1975.
- ^ [1] Arhivirano na sajtu Wayback Machine (28. фебруар 2017) "Konstrukcijski elementi I", Tehnički fakultet Rijeka, Božidar Križan i Saša Zelenika, 2011.
- ^ "Tehnička enciklopedija" (Elementi strojeva), glavni urednik Hrvoje Požar, Grafički zavod Hrvatske, 1987.
- ^ „Three workers securing a rivet”. NYPL Digital Collections. Архивирано из оригинала 2014-10-06. г.
- ^ Blind Rivets, August 1942, Popular Science Архивирано 2018-01-26 на сајту Wayback Machine early article that explains how they work
- ^ Zakivanje, [2] "Hrvatska enciklopedija", Leksikografski zavod Miroslav Krleža, www.enciklopedija.hr, 2018.
- ^ [3] Архивирано на сајту Wayback Machine (31. januar 2012) "Elementi strojeva", Fakultet elektrotehnike, strojarstva i brodogradnje Split, Prof. dr. sc. Damir Jelaska, 2011.
Literatura
uredi- Skripte o mašinskim elementima, univerziteti u Novom Sadu i Mostaru.
- Smith, Carroll (1990). Carroll Smith's Nuts, Bolts, Fasteners, and Plumbing Handbook. MotorBooks/MBI Publishing Company. str. 112. ISBN 978-0-87938-406-7.
- Collins, Jack A.; Staab, George H.; Busby, Henry R. (2002), Mechanical Design of Machine Elements and Machines, Wiley, ISBN 0-471-03307-3.
- Oberg, Erik; Jones, Franklin D.; McCauley, Christopher J.; Heald, Ricardo M. (2004), Machinery's Handbook (27th izd.), Industrial Press, ISBN 978-0-8311-2700-8.
- Minimum Thread Engagement Formula and Calculation ISO, Pristupljeno 2010-02-08.
- Segui, William T. (2007). Steel Design (4th izd.). Toronto: Thomson. ISBN 978-0-495-24471-4.
Spoljašnje veze
uredi- Mašinski elementi, univerzitet u Mostaru, pdf
- Mašinski elementi, univerzitet u Novom Sadu, pdf
- „Rivet”. Encyclopædia Britannica (na jeziku: engleski). 23 (11 izd.). 1911.
- Popular Science, November 1941, "Self-Setting Explosive Rivet Speeds Warplane Building" system used by both the US and Germany in World War Two for aircraft assembly – see bottom half of page
- Four Methods of Flush Riveting, film made by Disney Studios during World War Two
- "Hold Everything", February 1946, Popular Science new rivet types developed during World War Two
- "Blind Rivets they get it all together". Popular Science, October 1975, pp. 126–128.
- "RMS Titanic Remembered" – The Lads in the Shipyard